Sinterflex facade cladding is a modern exterior cladding material consisting of thin and lightweight ceramic panels used in contemporary buildings. It is increasingly preferred in architectural projects due to its superior technical features and aesthetic advantages. It offers a more durable, long-lasting and environmentally friendly alternative compared to traditional facade cladding materials.
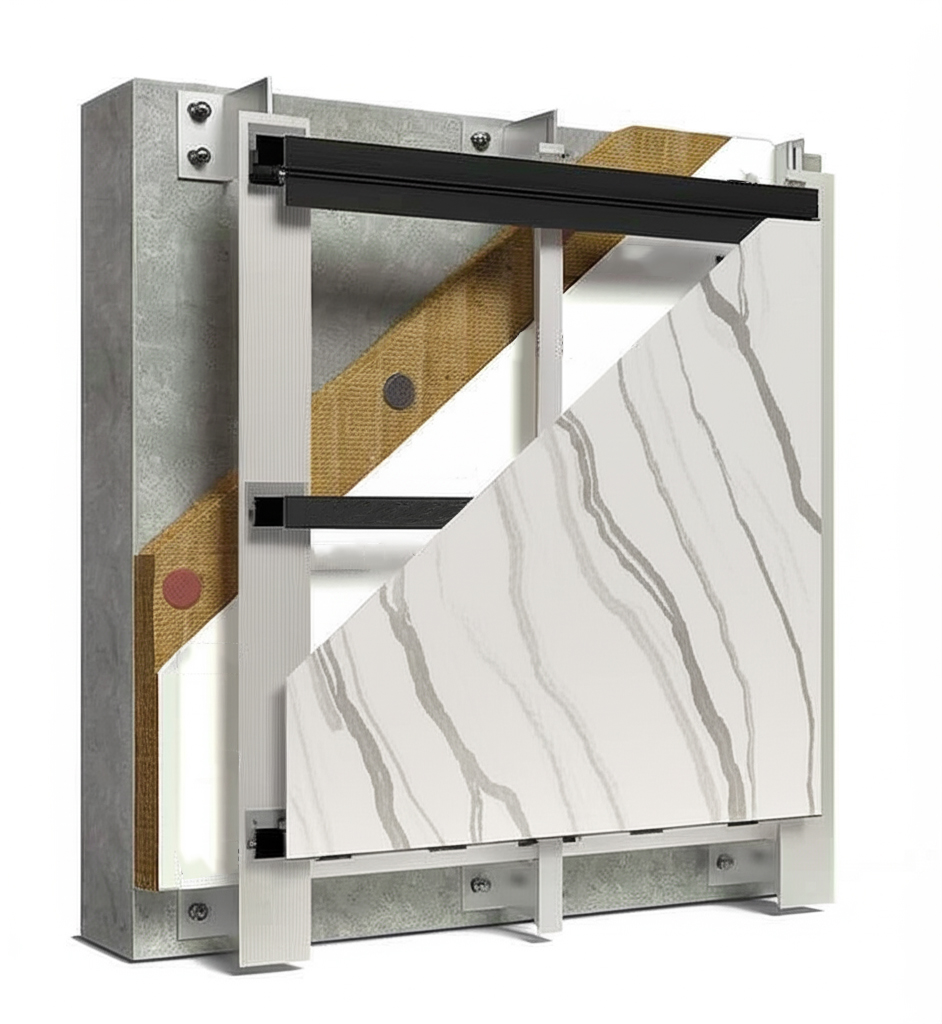
1- Thin and Lightweight Structure:
- Typically available in thicknesses ranging from 3 mm to 5 mm.
- Despite being large-format panels, its lightweight structure does not put extra load on the supporting system.
2- High Durability:
- Highly resistant to UV rays, scratches, impacts, and chemicals.
- Can withstand outdoor conditions for many years without deformation.
3- Waterproof and Moisture-Resistant:
- Has a water absorption rate below 0.1%, making it highly resistant to moisture.
- Resistant to rain, humidity, and frost, making it a reliable choice for exterior facades.
4- Fire-Resistant:
- It is a non-combustible material and maintains its physical form even when exposed to high temperatures.
- Complies with fire safety regulations, making it a safe facade cladding option.
5- Eco-Friendly:
- Made from recyclable materials.
- Manufactured using environmentally friendly technologies that do not harm nature.
6- Aesthetic Variety:
- Available in various designs and colors, including wood, natural stone, concrete, and marble textures.
- Its minimalist and modern appearance provides architects with extensive design freedom.
Exterior and Interior Application Areas:
- Creates a modern and stylish exterior surface for commercial and residential projects.
- Allows buildings to breathe with ventilated facade systems.
- Frequently preferred in metro stations, hospitals, airports, laboratories, and public transportation projects due to its durability and easy-to-clean properties.
How to Install Sinterflex Facade Cladding?
The installation of Sinterflex facade cladding should be carried out in accordance with the architectural structure and technical requirements of the building. To ensure a long-lasting and durable installation process, the following steps must be followed:
1. Project Analysis and Construction Selection
Every successful installation process begins with a detailed project analysis. First:
- The building’s load-bearing system and facade structure are examined.
- Climate conditions and environmental factors are taken into account.
- The substructure material (aluminum, steel, or stainless steel) is determined.
2. Infrastructure Preparation
Proper infrastructure preparation is crucial for a solid and long-lasting installation:
- The facade surface is inspected, and necessary reinforcements are applied.
- In ventilated systems, the substructure is mounted appropriately onto the building surface.
- The alignment of the supporting profiles is measured and adjusted using laser systems.
3. Panel Cutting and Preparation
For a perfect fit, Sinterflex panels undergo precise cutting and processing:
- Panels are cut to size with high-precision CNC machines.
- Drilling and edge finishing processes are carried out.
- Surface protection measures are applied, and the panels are made ready for installation.
4. Installation Methods
Two main installation methods are used depending on the system chosen:
A) Mechanical Installation (Ventilated Facade System)
- Panels are fixed to the supporting structure with stainless steel or aluminum clips.
- Expansion and contraction gaps are left to accommodate thermal changes.
- The horizontal and vertical alignment of the panels is meticulously checked before securing them.
B) Adhesive Installation (Direct Mounting)
- Panels are secured to the surface using high-strength elastic adhesives.
- The mounting surface is cleaned and primed beforehand.
- Pressure is applied to ensure strong adhesion, and the drying time is observed.
5. Final Checks and Cleaning
- All installation points and connections are reviewed for safety.
- Joint gaps are filled with special sealant materials for aesthetic and durability.
- Any remaining adhesive or installation residues on the panel surfaces are cleaned to ensure a flawless appearance.
SINTERFLEX FEATURES
SINTERFLEX is a term used in the ceramic industry for flexible, large-format, and thin ceramic slabs. It is commonly preferred for interior and exterior facade applications. Here are the key technical features of SINTERFLEX:
1. Material Properties:
- Manufacturing Process: Sintering (high-temperature pressing and firing)
- Raw Materials: Natural minerals, quartz, feldspar, and clay
- Surface Types: Matte, glossy, satin, or textured surface options
2. Physical and Mechanical Properties:
- Thickness: 3 mm, 5 mm, 6 mm, 12 mm (varies depending on application)
- Weight: Lighter than traditional ceramics (e.g., approximately 7 kg/m² for 3 mm thickness)
- Dimensions: Produced in large slabs (typically 1000x3000 mm, 1200x3600 mm, etc.)
- Flexibility: Provides a certain degree of flexibility due to its thin structure
3. Durability and Resistance:
- Scratch Resistance: High surface hardness (7+ on the MOHS hardness scale)
- Chemical Resistance: Resistant to acids, bases, and detergents
- UV Resistance: Does not fade or change color when exposed to sunlight
- Water Absorption Rate: Less than 0.1% (virtually waterproof)
- Heat Resistance: Withstands high temperatures, non-combustible material
- Fire Resistance: A1 fire-rated (according to EN 13501-1 standard). Resistant to high temperatures and does not emit toxic gases during a fire.
- Impact and Bending Strength: Despite being lightweight and thin, it is highly durable.